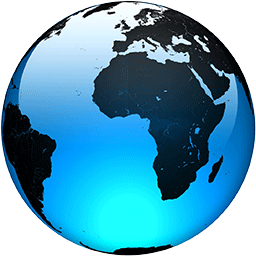
Greenland Minerals tests boost recoveries with aim to meet looming surge in rare earth demand
Greenland Minerals Ltd (ASX:GGG) (OTCMKTS:GDLNF) continues to optimise the Kvanefjeld Rare Earth Project in Greenland with advanced flotation test-work delivering strong results and increasing overall rare earth recoveries. This progress comes as the company looks to become an important new supplier to meet the looming surge in rare earth demand to serve new technologies aimed at providing a cleaner energy future. Test-work proves positive Recent locked cycle flotation test-work has produced rare earth mineral concentrate in excess of 23% rare earth oxide (REO). The tests have seen rare earth recoveries in mineral concentrate increased to 85% from 80% with light REO recovery of 87% and heavy REO recovery of 68%. “Strong progress” Managing director Dr John Mair said: “Technical work programs on Kvanefjeld have delivered strong progress through 2020, with a focus on continued development of the flotation circuit, and impurity removal in the refinery circuit. “The results of advanced locked cycle flotation test-work confirm the efficiency and effectiveness of the optimised circuit with a high upgrade ratio and further increases in both light and heavy rare earth recoveries.” Shares higher Shares have been almost 4% higher to 27 cents and are up from 12 cents at the market close on June 23. Greenland Minerals continues to be highly active across a number of fronts with a major milestone recently achieved on permitting with ongoing progress in-country. The company’s in-country presence was recently strengthened through a new key appointment in July with Jørn Skov Nielsen appointed executive general manager. Technical progress Technical progress is being made through close collaboration between GML’s technical team in Perth and rare earth specialists Shenghe Resources Holding Co Ltd, the company’s largest shareholder with 10.5%. This includes the locked cycle flotation test-work carried out at BTMR laboratories in China through 2020 and overseen by Shenghe Resources. The test-work closely represents the performance of a commercial circuit and builds on extensive single batch flotation and initial locked cycle tests. Results have been validated with check assays undertaken at SGS Laboratories in Perth, Australia, and an independent Chinese assay laboratory. This process development has progressed to the extent where conditions comparable to that of a commercial plant are to be tested. Multiple test cycles The latest locked cycle test-work completed multiple cycles of tests using the planned commercial circuit. Critically, the test included recycling of process water to determine the impact of residual reagents in solution on flotation performance. This is a significantly closer representation of the commercial flowsheet than previous test-work and further de-risks the process. The optimised test utilised eight full flowsheet cycles to ensure a steady-state was achieved. Samples were taken over the whole flowsheet during the eighth cycle to provide a ‘snapshot’ of the circuit performance. Key parameters Key parameters of locked cycle flotation test-work: Rare earth feed grade = 1.5% rare earth oxide (REO); Flotation concentrate grade = 23.3% REO; % Mass reporting to concentrate = 5.4%; Light REO recovery = 87%; Heavy REO recovery = 68%; and Total REO recovery = 85% (previously 80%). The results confirm the outstanding performance of the optimised flotation circuit, with the ability to concentrate the rare earths into a much smaller mass than that of the original ore, allowing for a small refinery circuit for hydrometallurgical treatment. The unique rare earth minerals can be effectively processed in a single-stage atmospheric acid leach circuit in which all impurities can be managed, allowing for the production and export of a clean intermediate rare earth product. “Well-positioned” Mair said: “Kvanefjeld’s unique and favourable metallurgy, combined with large, low-cost output of all critical magnet rare earths (Nd, Pr, Tb, Dy) has Greenland well-positioned to be an important new supplier to meet the looming surge in rare earth demand.” Fluoride removal Continued development of the flotation circuit has also involved further investigation of the removal of excess fluoride ions in the process water. The fluoride comes from the soluble mineral villiaumite which is present in the ore. Configuration changes to the flotation circuit allow for greater fluoride removal prior to the main rare earth flotation stage with the fluoride to be recovered as fluorspar (metspar). This results in lower flotation reagent consumption and a substantial reduction of fluoride in tailings which mitigates environmental impacts and benefits environmental management. Further enhancements in fluoride removal are expected with ongoing process development.
Full Article