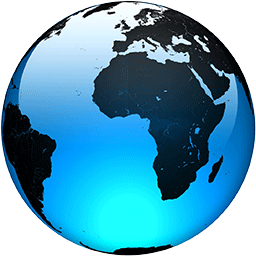
EcoGraf’s purification process confirms superior performance of graphite source in battery material
EcoGraf Limited’s (ASX:EGR) (FRA:FMK) additional results from electrochemical analysis of preferred feedstocks for its proposed EcoGraf™ battery graphite facility in Kwinana, Western Australia, have demonstrated superior performance against existing material used in the lithium-ion battery market. The results confirm that battery graphite produced from these feedstocks can be expected to deliver superior performance when converted into battery graphite using the EcoGraf™ process. This work demonstrates the importance of battery graphite crystallinity, which has a direct effect on battery performance factors such as power output, battery life and charging capability. As a result, EGR's battery products are uniquely positioned as a superior and cost-competitive alternative material for the battery anode supply chain. The electrochemical test work was carried out at a leading independent German Research Institute, which works with major lithium-ion battery and electric vehicle manufacturers. EcoGraf™ process confirmed The results confirmed the preferred EcoGraf™ feedstocks, including the company’s Epanko material, consistently outperformed existing material under various electrochemical test conditions. The test work also confirmed that the physical properties, mineralogy, and degree of crystallinity of each natural graphite source directly affects battery anode performance within the lithium-ion battery. This is a significant observation as each graphite source has its own unique geological setting, with some sources unable to meet the strict specifications of the battery manufacturers. Crystallinity is an important property in the lithium-ion battery as the level of crystallinity affects the electrochemical performance. In natural graphite deposits, crystallinity is determined by the geological setting and the extent of natural temperature, pressure forces and time that has been applied in the formation of the graphitic rocks. Higher crystallinity results from higher temperature and rock pressures for a longer period of time. Electrochemical test work was carried out on uncoated natural graphite after processing using EcoGraf™ purification, with all parameters remaining constant to provide relative results. Testing measured the specific capacity (mAh/g) of each graphite product to assess its battery performance. Clean energy with high purity graphite EcoGraf is building a vertically integrated business to produce high purity graphite for the lithium-ion battery market. Its new state-of-the-art processing facility in Western Australia will manufacture spherical graphite products for export to Asia, Europe and North America using a superior, environmentally responsible purification technology to provide customers with sustainably produced, high-performance battery anode graphite. The battery graphite production base will be expanded over time to include additional facilities in Europe and North America to support the global transition to clean, renewable energy in the coming decade. EcoGraf’s breakthrough recovery of graphite from recycled batteries using its EcoGraf™ process will enable the recycling industry to reduce battery waste and use recycled graphite to improve battery lifecycle efficiency. EcoGraf is also developing the TanzGraphite natural flake graphite business, commencing with the Epanko Graphite Project, which will supply additional feedstock for the spherical graphite processing facilities and provide customers with a long term supply of high-quality graphite products for industrial applications such as refractories, recarburisers and lubricants.
Full Article