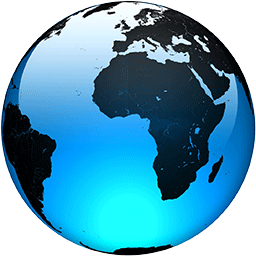
Opinion: How Jaguar will compete with Bentley
Jaguar engineering boss Philip Koehn was heavily involved in the Rolls-Royce Phantom 8
Changes in production technique will have cars produced at a lower volume and higher price
Jaguar’s engineering boss of the past 18 months, Philip Koehn, first came to notice five years ago as chief engineer of Rolls-Royce, based at the time in BMW’s aluminium body-in-white plant at Dingolfing, near Munich. He had joined BMW as a dynamics engineer, he told us, but had moved to specialise in the design of structures.
In an exclusive Autocar story timed for the launch of the new Rolls-Royce Phantom 8, Koehn revealed how he was leading a team pioneering a new, highly flexible aluminium spaceframe chassis that would provide underpinnings not only for the Phantom but also for four other forthcoming Rolls-Royce models, all with different body and mechanical layouts, powered by both ICE and EV powertrains.
That experience, and Koehn’s comments about it back in 2017, give a valuable insight into how Jaguar is tackling its own huge challenge: of moving, in price and exclusivity terms, from being a BMW to Bentley competitor, doing it in time to show a concept model in 2024 and to have production cars in showrooms in 2025.
Back in 2017, Koehn explained how and why Rolls-Royce had moved from using a BMW 7 Series floorpan for the more workaday of its two saloons, the Ghost, even though the former solution had originally been viewed as the more economically viable, because it could take advantages of economies of scale. “By using the 7 Series, we were asking components to deliver things they weren’t intended to, which meant the promised economies of scale weren’t as viable as we thought,” he said.
The solution, in which Koehn was a leading pioneer, was to design, build and prove a brand-new aluminium spaceframe along the lines of that introduced for BMW’s original Phantom VII of 2003 but much more flexible. The new structure would consist again of aluminium longitudinals attached to lightweight castings for the more complex parts, such as suspension mounts and chassis corners.
Even for low-volume cars, he came to realise, economies of scale could be delivered if you committed to ordering from suppliers very large batches of components that could be utilised for many years. Parts cited included front and rear strut castings, rear subframes and crash-absorbing chassis longitudinals. With foresight, he told us, even 4000-per-year Rolls-Royce could forward-order components in batches of up to 70,000 – around 15 years’ supply.
Parts likely to vary much more in dimensions – such as floorpans, A-pillars and bulkheads – would be in shorter supply, although Rolls-Royce still held an advantage, because its models tended to last longer in production than most.
There’s no confirmation yet from inside Jaguar Land Rover that Koehn and his teams are working precisely this way, but their plans echo those of Rolls-Royce very closely. They will build cars in aluminium and in much lower volume than before. They will sell multiple models (three, we understand), all based on a highly flexible architecture and at higher prices than previous Jaguars. The Leaping Car is moving unashamedly into the luxury car realm.
When Koehn revealed his Rolls-Royce plan back in 2017, he made no bones that he relished the chance to build luxury cars in a new way. “I always wanted to be a pioneering kind of guy rather than an optimiser,” he explained, describing the Rolls-Royce programme as the chance of a lifetime. With Jaguar, it seems he has a second one.