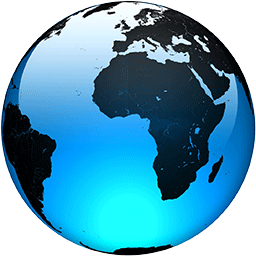
The UK company that makes just-in-time car manufacturing work
Parts and supplies are being delivered, sometimes cross-continent, in less than a day to keep production running
It’s the firm you’ve never heard of, but one that’s growing in importance across the automotive sector. Why? Because Priority Freight is the car maker’s “under the radar” crisis savour.
The Dover-based business, which has three UK and six mainland European bases, takes on a “vast” number of enquiries every day – enquiries it turns around within 15 minutes of the call coming in. Most are from tier one and two OEMs.
“We are all about speed and about winning time back for the customer,” said commercial director Andrew Austin.
“They come to us in the event of an issue, normally that their main transport contractors were unable to have the flexibility to cross borders, cross time zones with the speed that is required. We support clients in being able to get their production going.”
He added: “In reality we can be moving products from Asia and be back inbound within 24 hours. So the speed involved is incredibly dramatic.”
It’s this level of speed that has given the firm a strong reputation among those within automotive – a sector that makes up most of its business – as the reliable go-to when issues occur.
This can be by air, in the form of anything from chartered flights to a passenger courier, or by land with two drivers who “sleep and switch” so it’s only fuel fill-ups that will pause their journey. The firm has a fleet of more than 6000 vehicles.
In a recent commission, the firm couriered 300 semiconductors, worth £110,000, 600 miles from Birmingham to Le Mans in 20 hours. Within one hour of the enquiry, customs papers were completed and a driver was picking up the goods.
Although they're needed, they’re not always wanted. “We are sometimes the knights in shining armour, and sometimes the unnecessary expenditure clients really begrudge,” said Austin.
“To admit to having to use expedited or emergency freight shipments in some ways is an admission of the supply chain failing.”
But, he adds, despite the firm’s high cost – it deals with everything from the “first to the last mile” – this can sometimes be cheaper than the money lost due to production potentially needing to be shut down due to a lack of parts.
“If one shift – if a factory operates a three-shift system – identifies a shortage of parts, we can have the parts in place for the start of the second shift, so they don't have that downtime,” said Austin.
“And the reality then is that they're making a simple economic permutation. They're saying: 'If we have four thousand guys standing around doing nothing, this is costing us, let's say, £6000 per hour.’ Then there’s the economic justification to choose us.”
One job illustrates this, when an unnamed European-based automotive manufacturer called for help as issues – such as the Covid-19 pandemic – were gradually slowing the supply of parts to a point where a plant shutdown was imminent.
For production to continue, they required daily collection of parts from up to 30 UK and EU suppliers, but information on how much was being collected was limited.
Over two weeks, the firm shipped in 50,000kg of air freight, as well 40 road shipments, 24 hours a day. In effect, Priority Freight became the manufacturer’s dedicated supply chain courier.
Austin says this is just one example of why the firm is so important to some clients' supply chain that some car makers are now budgeting them into their annual costings
“The relationships [between us and our clients] has changer since Covid, because often people build us into their equations now,” said Austin. “But we still normally represent an emergency spend or a discretionary spend that is often focused on the need rather than the planned need.”
Because of that, discretion is key. “We have internal relationships with our clients where we tend not to make big stories publicising ourselves and naming the clients we are supporting because it can be embarrassing to them.”
A key criticism the firm faces is the way in which it operates, self-confessed to not be very environmentally friendly. But, as the world moves forward, it concedes it must too. “Sustainability is something that, as a business, we take extremely seriously,” said air chartering boss Steve Downing.
“We have a team of people that are specifically looking at sustainability and working with our clients on the impact [the work we do for them] is having. That's something that we're driving forward as well and various initiatives that we're putting in place to help our clients.”
Austin added: “We cannot claim to be environmentally friendly, but we're an emergency freight movement firm. But what we consciously do is put as light a touch as we can on it: the most efficient aircraft, the most efficient engines, and use solutions that are the least harmful.”