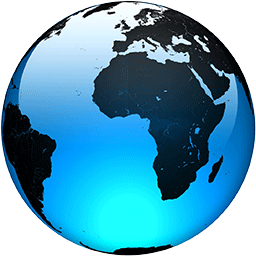
First Cobalt recovers nickel, copper and lithium from battery recycling test work
First Cobalt Corp. has successfully extracted nickel, cobalt, copper, manganese, lithium and graphite from a “black mass” product recovered from recycled batteries. Black mass represents the main chemical composition of the battery and is obtained after the removal of the mechanical housing of the battery. In a statement, the company said work is now underway to leverage the existing operating permits, flowsheet, and equipment at its Canadian hydrometallurgical refinery to become the first facility to recycle battery materials on a large scale for reintroduction into the electric vehicle battery supply chain. READ: First Cobalt says recommissioning of battery metals plant near Toronto progressing as scheduled To date, First Cobalt said there is no operating facility in North America that can recover nickel, cobalt, copper, lithium, graphite and manganese from black mass on a large scale, continuous production basis. The company's refinery in Canada has existing refining capabilities to produce separate products containing nickel, cobalt, copper, and manganese. With flowsheet modifications, recovery of lithium and graphite can also be achieved. First Cobalt said metallurgical test work was conducted by SGS Labs on black mass material provided by upstream battery recyclers in the US and Europe. Bench-scale testing has demonstrated expected extractions of lithium, nickel, cobalt, copper, manganese and graphite. Also, a global engineering firm has been retained to study the leaching of black mass within the existing refinery to produce nickel, cobalt, copper and manganese products using the existing flowsheet and to produce lithium and graphite products, with recommended modifications. Completion of the engineering study is expected in the fourth quarter. Upon successful completion of the study, the company intends to process black mass at the refinery facility on a pilot basis. First Cobalt said its near-term strategy is to leverage its existing processing facilities to process black mass and recover payable metals. Longer term, the company intends to produce "battery-grade" materials for reintroduction into the electric vehicle supply chain. Discussions also have been initiated with provincial regulatory authorities to permit the processing of black mass at its facility. 'Important step' "Demonstrating our ability to recycle lithium-ion batteries is an important step in our journey to be the most sustainable producer of battery materials," said First Cobalt CEO Trent Mell. "There are many producers of black mass in the western world but few environmentally friendly options to then refine the product into battery-grade material, given the capital expenditure required and the permitting timeline associated with building a hydrometallurgical facility such as ours. We intend to capitalize on this first-mover advantage and leverage our position as an ultra-low carbon operation." The company said it is modifying the flowsheet under a Phase 1 expansion at its facility to refine a third-party cobalt hydroxide intermediate product into a high-purity, battery-grade cobalt sulfate suitable for the electric vehicle market. Today, around 80% of cobalt sulfate is made in China and there is no production in North America. Under a Phase 2 expansion, the refinery is expected to process black mass feed from recycled batteries. Longer term, the company's vision is to establish a Battery Park that would include large-scale production of nickel sulfate and the co-location of a battery precursor manufacturer. Contact the author: patrick@proactiveinvestors.com Follow him on Twitter @PatrickMGraham
Full Article